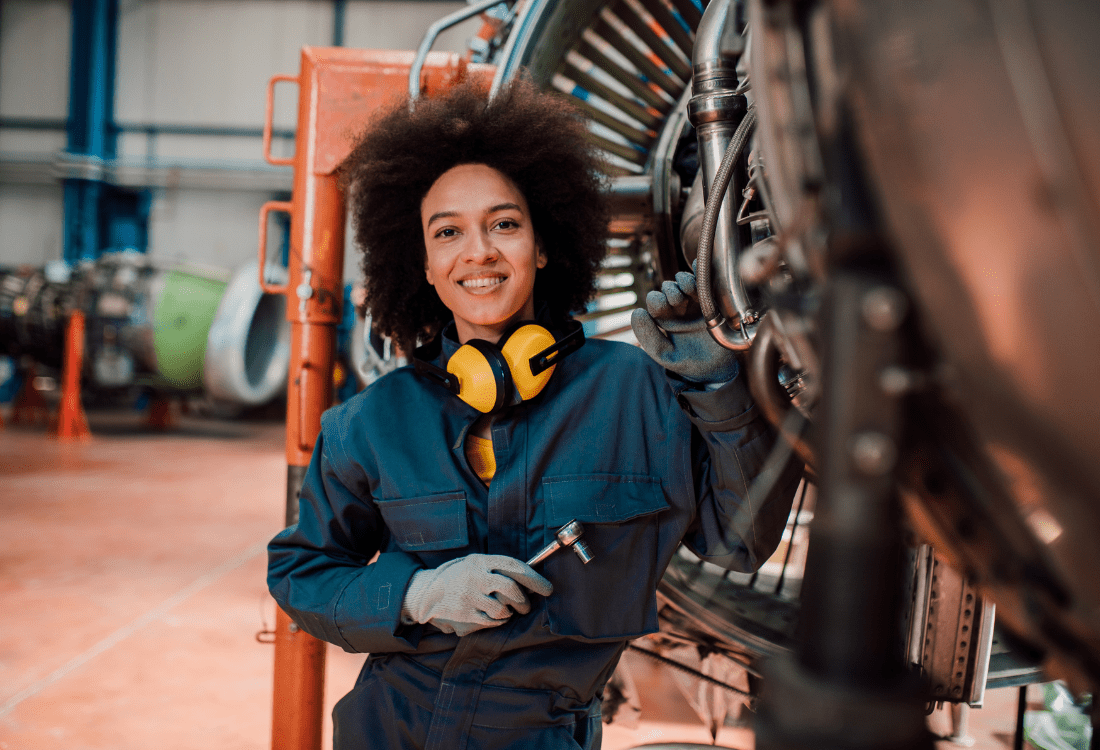
Understanding Couplings: Rigid Vs Flexible Explained
Couplings connect shafts and transmit power between motors, pumps, generators, and more. Available in rigid and flexible versions, choosing the right type is critical for any application, and understanding how these two coupling types differ is key to success. But what are the main differences between the two types, and how does this affect performance?
A Quick Look At Flexible Couplings
Flexible couplings are designed to accommodate some degree of misalignment between the shafts they connect. This flexibility allows the coupling to adapt to shifts from factors like manufacturing tolerances, temperature changes, or settling foundations.
Common flexible coupling designs, such as gear, grid, bellows, and disc types, use elastic elements or sliding surfaces to permit these degrees of shaft misalignment - angular, parallel offset, axial motion, or combinations. This protects other drivetrain components, like bearings, from increased wear and tear due to misalignment.
Where Are Rigid Couplings Used And What Are They?
In contrast, rigid couplings create a solid, high-strength connection between two shafts. With little or no flexibility, rigid couplings can transmit very high torques and rotational speeds. They align the shafts precisely, maintaining positional accuracy.
Rigid couplings, such as sleeve, clamp, or flanged types, are ideal for machine tools, rolling mills, test rigs, and other high-torque situations where precision shaft alignment is necessary. However, no movement or flex is permitted once installed.
Rigid Coupling Vs Flexible Coupling: How They Differ
Rigid and flexible couplings have several key differences that make them suitable for different applications. For example:
-
Misalignment - Flexible couplings permit angular, parallel, and axial shaft misalignments through internal elasticity. Rigid couplings do not tolerate any shaft misalignment.
-
Torque capacity - Rigid couplings are typically capable of transmitting higher levels of torque given their solid shaft attachments. Flexible couplings see some derating at higher torques.
-
Acceleration/deceleration - Flexible couplings help dampen torsional vibrations from acceleration or shock loading. Rigid couplings immediately transfer these forces.
-
Assembly - Rigid couplings require precision shaft alignment before installation. Flexible models can accommodate some level of misalignment during assembly.
Rigid Vs Flexible Coupling: Factors To Consider When Choosing Between Them
When choosing a coupling, the following factors will help you determine which type best fits the application:
-
Torque requirements - If very high torque transmission is needed, rigid couplings are usually a better option, as flexible versions experience torque derating.
-
Misalignment allowance - If any shaft misalignment is expected or permissible, flexible couplings should be used to accommodate this.
-
Rotation precision - Where perfect shaft alignment and positional accuracy are mandatory, rigid couplings help maintain the necessary precision.
-
Operating conditions - Temperature changes, vibration, shock loads, and other real-world conditions make flexible couplings preferable to compensate.
-
Space constraints - Flexible couplings often require more space than rigid versions due to the various internal flexible elements, such as tyres, rubber elements or bellows.
Choose Between Flexible And Rigid Couplings With BTL
Understanding the core differences between rigid and flexible couplings allows OEM designers to make informed, performance-based coupling selections. Whether you need couplings for high-precision torque transmission or to accommodate real-world shaft misalignment, focusing on the requirements of the application will ensure you make the right choice.
For some of the best couplings on the market, please download the BTL Power Transmission Catalogue or get in touch!
Image Source: Canva