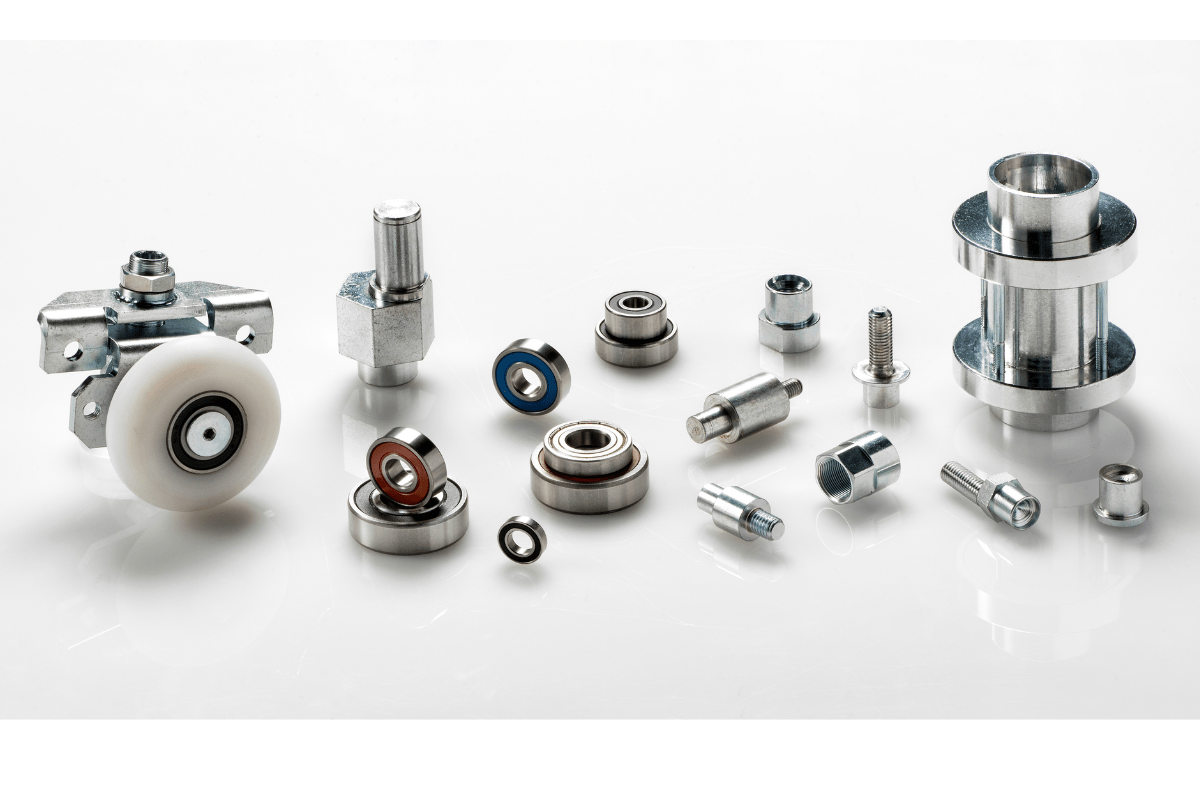
7 Reasons To Use CNC Precision Turned Components In Your Power Transmission Systems
There are several advantages of using precision turned components in your power transmission systems, and although the upfront costs may be higher, the additional investment will usually pay for itself in terms of efficiency, productivity, and reduced maintenance and downtime.
What Is A ‘Precision’ Turned Component?
A precision turned component is any part that has been machined to an extremely tight tolerance. At BTL-UK, for instance, we use CNC machining to produce a wide array of complex parts, such as the bearings, linkages, and power transmission components used in automotive manufacturing and other commercial sectors. Precision components may be purchased from a stock catalogue or designed individually to meet a bespoke need.
How Are Precision Turned Components Made?
Precision turned components are created by turning a cylindrical part on a CNC lathe or machine. The component is then cut into the required size and shape by means of cutting tools, end mills, and drills, resulting in a highly precise component to meet the performance requirements of demanding commercial applications.
Advantages Of Precision Turned Parts
1. Cost-Effective (Save On Energy)
CNC precision turned components can reduce your operating energy costs by minimising friction and waste heat, with the ability to generate the same power output while running at lower speeds.
2. Improves Production Efficiency
Deploying CNC precision turned components within your application can optimise your production processes and increase overall efficiency, by improving accuracy and minimising human error.
3. Capable Of Manufacturing High-Quality Parts With A Wide Range Of Materials
Investing in precision turned parts also gives you greater control over the materials and size configurations of your parts, with a variety of materials including steel, titanium, aluminium, chromium, or even types of thermoplastic or acrylic – without compromising on quality, accuracy, or lead times.
4. Dimensional Accuracy And Reduced Human Error
CNC machining is capable of sustaining tight tolerances across production requirements of any volume, maintaining dimensional accuracy throughout the entire production process. This helps reduce human error and lowers costs by rationalising the use of materials and minimising wastage, which can lower the unit cost of CNC turned components across a production run – as well as simplifying the inspection and approval process.
5. High Repeatability
Precision turned components have high repeatability, which is essential for the production of identical parts in consumer applications. CNC machines can produce identical parts consistently over time across indefinite production runs, making them perfectly suited for mass production scenarios in which multiple pieces need to be machined to exacting specifications each time.
6. User Friendly And Safe
The accuracy and repeatability of CNC machined parts increases their user-friendliness and safety rating, lowering the risk of DOA components, premature mechanical failures and faults, and also saving you and your end-users money long-term on repairs and maintenance.
7. Low Wastage
CNC precision production allows manufacturers to optimise their use of precious raw materials, with savings that can be passed on to their customers without compromising on the quality and turnaround times for premium products.
Next steps – Request A Copy Of Our Free BTL-UK Product Catalogue
At BTL-UK, we manufacture and supply an extensive range of precision turned components for industrial and commercial power transmission systems. For full information about our current range, please click here to download a free copy of our 2023 product catalogue. We also offer a completely bespoke component design and machining service, so if you would like to discuss a project with one of our experienced CNC specialist, please call 01233 663340 today.
Image Source: Canva